What is Porosity in Welding: Usual Resources and Reliable Treatments
Wiki Article
The Scientific Research Behind Porosity: A Comprehensive Guide for Welders and Fabricators
Understanding the complex devices behind porosity in welding is essential for welders and producers making every effort for impeccable craftsmanship. From the make-up of the base products to the ins and outs of the welding procedure itself, a plethora of variables conspire to either exacerbate or reduce the existence of porosity.Comprehending Porosity in Welding
FIRST SENTENCE:
Examination of porosity in welding reveals crucial understandings right into the stability and quality of the weld joint. Porosity, characterized by the existence of cavities or spaces within the weld steel, is an usual problem in welding processes. These gaps, if not properly dealt with, can endanger the structural integrity and mechanical residential or commercial properties of the weld, leading to potential failings in the completed product.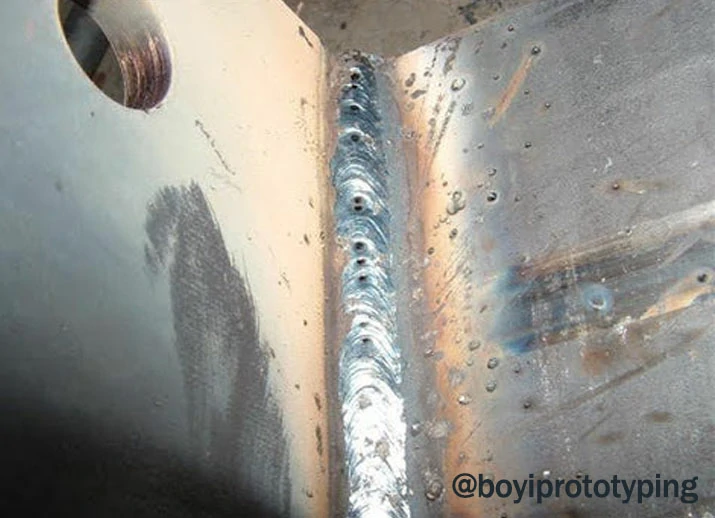
To find and measure porosity, non-destructive testing approaches such as ultrasonic screening or X-ray evaluation are frequently used. These methods enable the recognition of interior problems without compromising the honesty of the weld. By evaluating the size, form, and distribution of porosity within a weld, welders can make enlightened choices to improve their welding procedures and accomplish sounder weld joints.

Factors Affecting Porosity Development
The incident of porosity in welding is affected by a myriad of elements, varying from gas securing effectiveness to the ins and outs of welding criterion settings. Welding specifications, consisting of voltage, existing, travel speed, and electrode type, additionally influence porosity formation. The welding method utilized, such as gas steel arc welding (GMAW) or secured metal arc welding (SMAW), can influence porosity formation due to variants in warmth circulation and gas coverage - What is Porosity.Effects of Porosity on Weld Quality
Porosity formation substantially jeopardizes the architectural honesty and mechanical residential or commercial properties of welded joints. When porosity is existing in a weld, it produces gaps or dental caries within the product, reducing the overall strength of the joint. These voids serve as anxiety focus factors, making the weld a lot more prone to fracturing and failing under lots. The visibility of porosity additionally weakens the weld's resistance to corrosion, as the trapped air or gases within the voids can react with the surrounding environment, leading to deterioration in time. Additionally, porosity can hinder the weld's capability to endure pressure or impact, further jeopardizing the total top quality and integrity of the bonded structure. In vital applications such as aerospace, automobile, or structural use this link constructions, where safety and durability are extremely important, the destructive results of porosity on weld high quality can have severe consequences, stressing the value of lessening porosity through proper welding strategies and procedures.Techniques to Lessen Porosity
Furthermore, utilizing the ideal welding criteria, such as the correct voltage, current, and travel speed, is vital in protecting against porosity. Maintaining a consistent arc length and angle during welding description also assists minimize the probability of porosity.
In addition, choosing the ideal protecting gas and preserving appropriate gas circulation prices are necessary in decreasing porosity. Making use of the ideal welding strategy, such as back-stepping or utilizing a weaving motion, can also aid disperse heat equally and reduce the opportunities of porosity formation. Lastly, ensuring correct air flow in the welding atmosphere to remove any kind of possible resources of contamination is important for achieving porosity-free welds. By executing these strategies, welders can successfully reduce porosity and generate top notch welded joints.
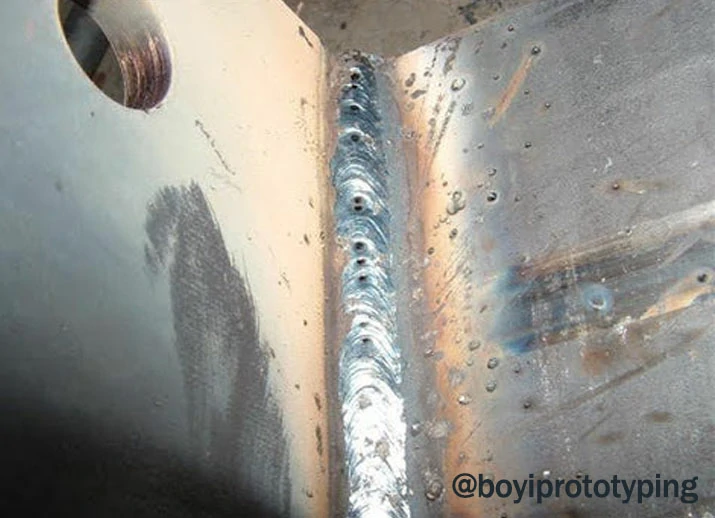
Advanced Solutions for Porosity Control
Carrying out advanced technologies and innovative approaches plays an essential function in achieving premium control over porosity in welding procedures. One advanced solution is the usage of sophisticated gas mixes. Securing gases like helium or a blend of argon and hydrogen can help in reducing porosity by giving much better arc stability and boosted gas coverage. Furthermore, using advanced welding methods such as pulsed MIG welding or changed atmosphere welding can likewise aid mitigate porosity problems.Another advanced option entails using advanced welding devices. For example, making use of equipment with built-in features like waveform control and sophisticated source of power can boost weld top quality and reduce porosity risks. Furthermore, the implementation of automated welding systems with precise control over parameters can considerably minimize porosity website link problems.
Furthermore, incorporating innovative surveillance and examination modern technologies such as real-time X-ray imaging or automated ultrasonic screening can help in finding porosity early in the welding procedure, permitting prompt corrective actions. In general, integrating these sophisticated options can considerably boost porosity control and boost the total top quality of bonded parts.
Verdict
To conclude, understanding the science behind porosity in welding is vital for welders and producers to produce high-grade welds. By recognizing the variables affecting porosity development and carrying out methods to lessen it, welders can enhance the overall weld quality. Advanced solutions for porosity control can further enhance the welding procedure and make certain a solid and dependable weld. It is important for welders to constantly educate themselves on porosity and apply finest techniques to accomplish optimum outcomes.Report this wiki page